Help & Advice > Product Guides > Lead Flashing
Lead flashing is a common material used in building projects for a variety of purposes, including repairs and waterproofing. However, there are multiple different types of lead with varying attributes and production processes. This guide will outline the similarities and differences between milled lead vs cast lead.
Table of contents:
Milled lead
Milled lead (also known as rolled lead) is manufactured under a highly automated process. This allows it to be produced to a consistent quality and size.
During the manufacturing process, a lead slab is constantly passed between two hydraulic rollers. This forms a sheet with precise consistency and thickness. This production method makes sure that each roll of lead is of a similar thickness along the entire length of the roll.
Buildings being constructed to a high standard may insist on the use of lead manufactured to BS EN 12588, the British Standard on lead and lead alloys. Milled lead is the only lead flashing produced to this standard, owing to the precision in the manufacturing process.
Cast lead
Cast lead (also known as machine cast lead) is manufactured by rotating a half-submerged water-cooled drum in a bath of molten lead. As the drum rotates, the hot molten lead sticks to the sides of the cold drum and solidifies. This is then peeled off the drum and onto a cutting bed.
This type of lead is different to milled lead in that the thickness is controlled by changing the depths that the roller is to be immersed, and the speed at which the drum rotates. This difference in production means that cast lead can never match the exact tolerance as that of milled lead. One benefit, however, is that this is more cost-effective due to the simpler production process.
Milled lead vs cast lead
Aside from the differences in manufacturing, there is little between the two products in usability. There is a preference towards milled lead with some specialist contractors who say that it is easier to work, less likely to have a brown tint and less likely to split.
Other tagged products
- SHOW MORESHOW LESS
Other tagged products
- SHOW MORESHOW LESS
Other tagged products
- SHOW MORESHOW LESS
Other tagged products
- SHOW MORESHOW LESS
Other tagged products
- SHOW MORESHOW LESS
Other tagged products
- SHOW MORESHOW LESS
Other tagged products
- SHOW MORESHOW LESS
Other tagged products
- SHOW MORESHOW LESS
Other tagged products
- SHOW MORESHOW LESS
Other tagged products
- SHOW MORESHOW LESS
Other tagged products
- SHOW MORESHOW LESS
Other tagged products
- SHOW MORESHOW LESS
Other tagged products
- SHOW MORESHOW LESS
Other tagged products
- SHOW MORESHOW LESS
Other tagged products
- SHOW MORESHOW LESS
Other tagged products
- SHOW MORESHOW LESS
Other tagged products
- SHOW MORESHOW LESS
Other tagged products
- SHOW MORESHOW LESS
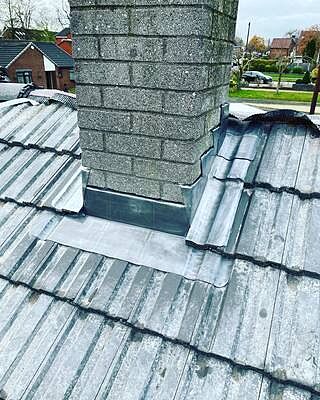
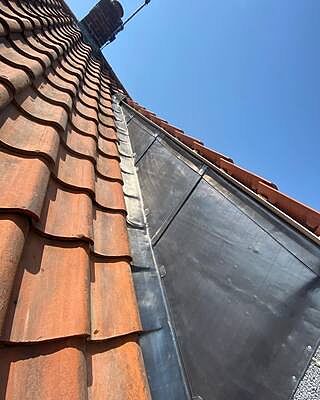
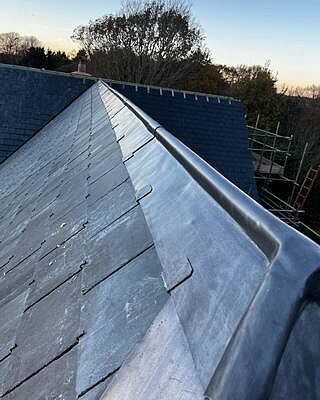
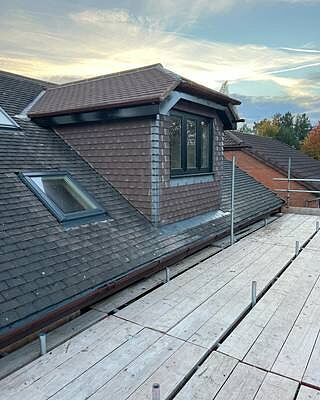
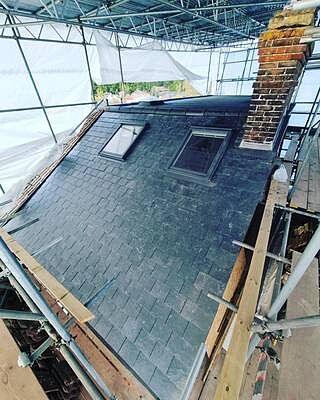
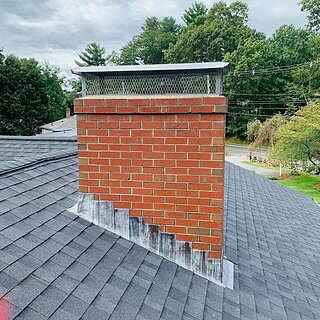
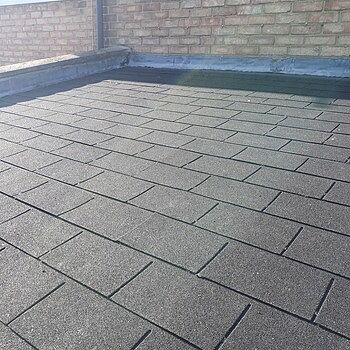
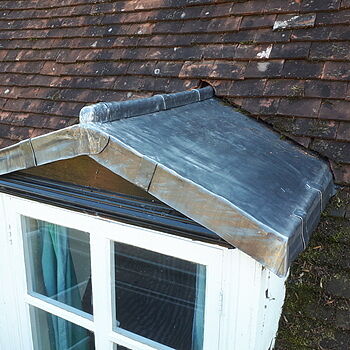
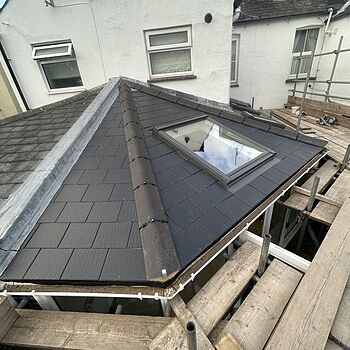
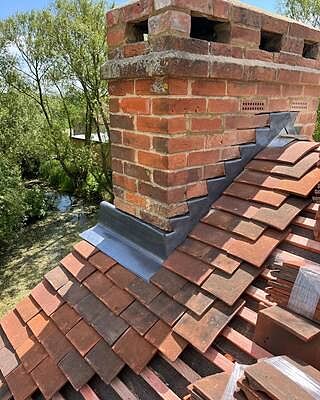
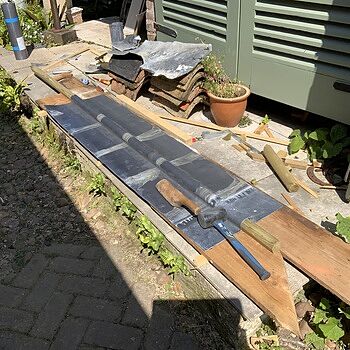
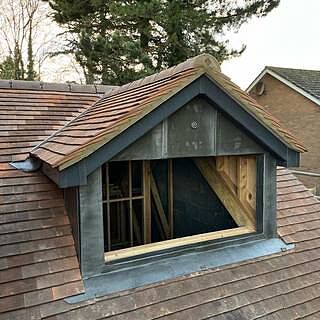
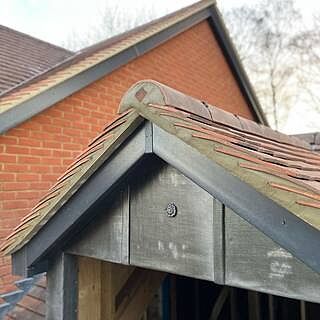
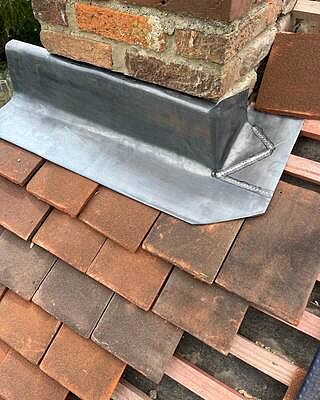
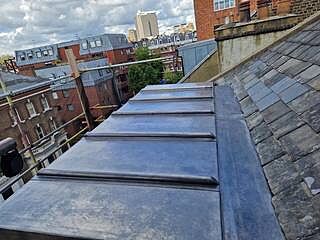
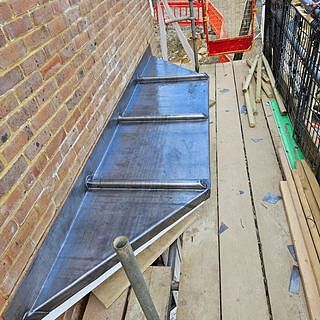
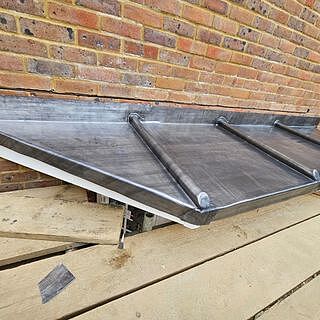
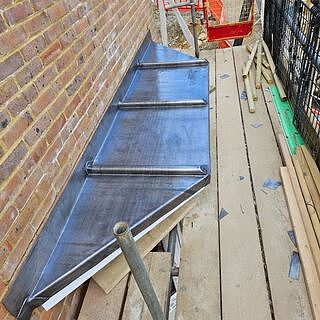
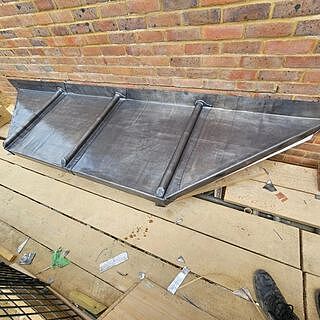
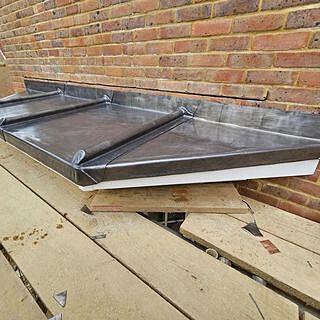
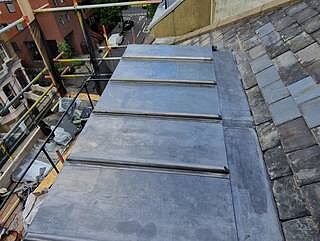
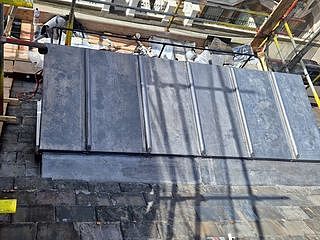
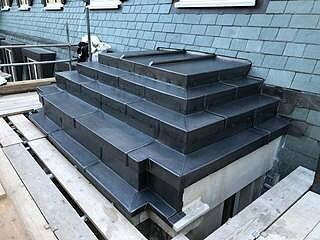
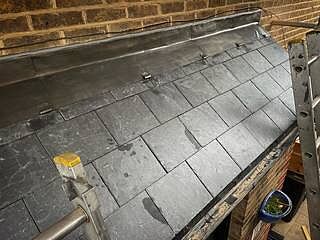
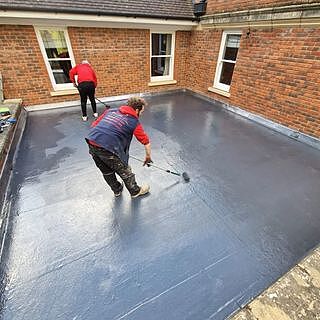
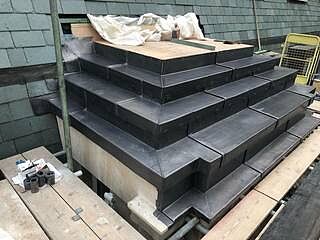
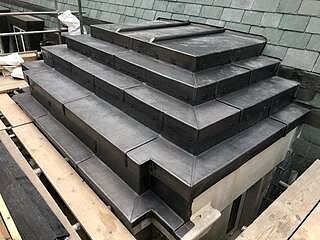
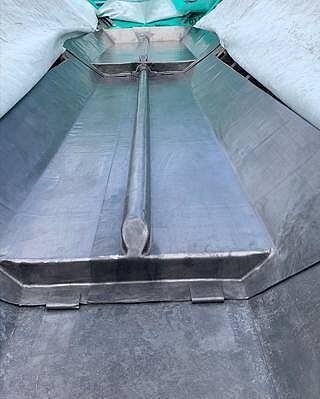
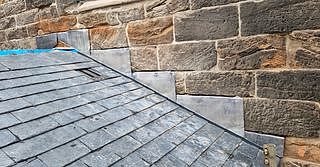
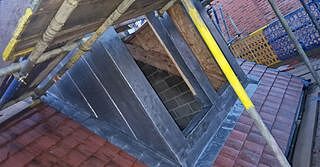
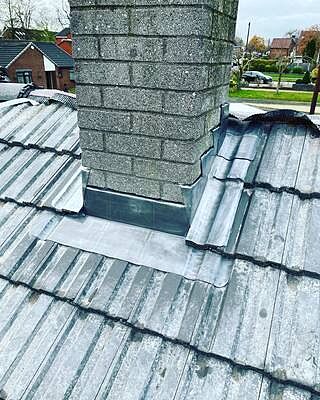
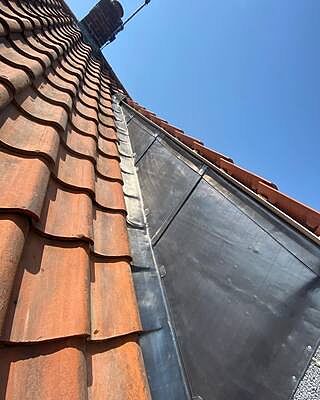
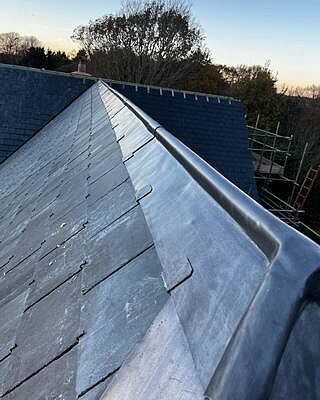
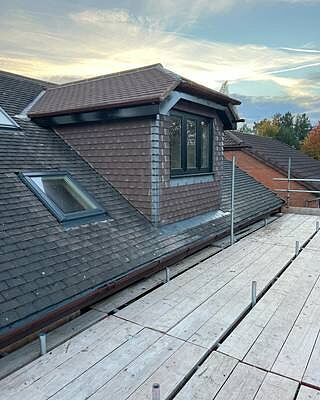
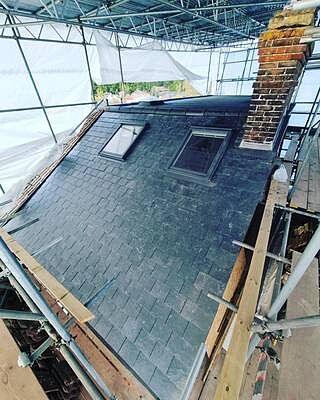
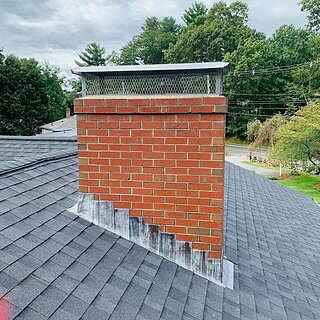
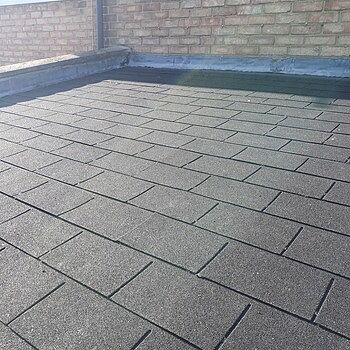
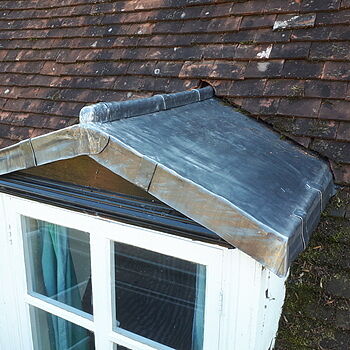
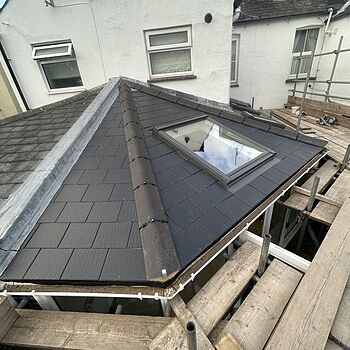
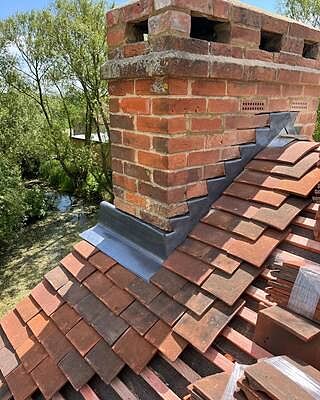
Was this guide useful?
Mentioned in this product guide:
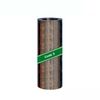
Calder Lead Code 3 Roofing Lead Flashing Roll - 150mm
from
£18.69 ex VAT
from
£22.43 Incl. VAT
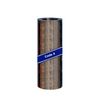
Calder Lead Code 4 Roofing Lead Flashing Roll - 300mm
from
£48.06 ex VAT
from
£57.67 Incl. VAT
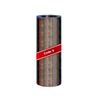
Calder Lead Code 5 Roofing Lead Flashing Roll - 450mm
from
£90.78 ex VAT
from
£108.94 Incl. VAT
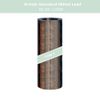
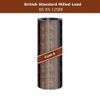
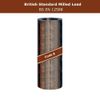